
3D打印助力中国航发出品高度集成化的发动机
宣布时间:
2023-01-11 12:43
飞机上的零件每减轻一点重量就将使飞机节省大宗的燃油消耗,以一架起飞重量达65吨的波音737 飞机为例,如果机身减轻一磅(约0.45千克),每年将节省数十万美元燃油本钱。
在前不久举行的第十八届北京航展中,中国航发集团展示了中国航发增材制造发动机项目所取得的轻量化发动机设计结果。选区激光熔化金属3D打印技术助力中国航发增材制造发动机项目制造了多个零部件,实现了发动机零件结构集成化设计,并实现了一体化打印。
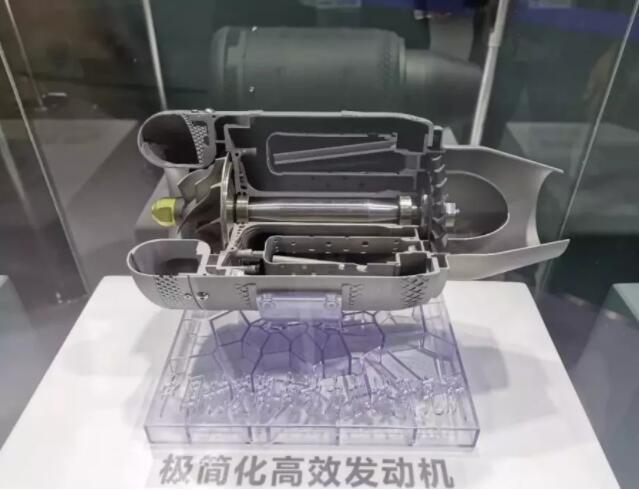
来源:铂力特
实现减重目标
中国航发增材制造发动机项目中的增材制造发动机零部件由铂力特使用BLT-S310设备制造。项目主要有两个立异点:
1. 建立了基于增材制造技术的发动机零件集成化设计技术,通过该集成化技术,研制了一型基于增材制造技术的高度集成化的小型涡喷发动机,零件集成率高达81%,降低发动机装配难度,提高发动机的可靠性和维修性;
2. 建立面向增材制造和拓扑优化技术的零件轻量化设计技术,在立异结构空心离心叶轮、空心涡轮轴及空心涡轮盘等优化设计有了重大突破,并接纳增材制造工艺实现了空心转子件的加工制备。
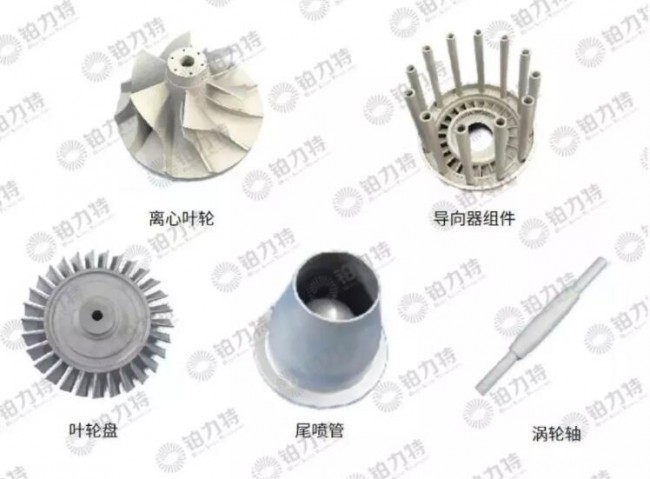
来源:铂力特
其中,导向器蒸发管组件、尾喷管均为薄壁结构,古板加工方法为多个零件组装而成,现接纳3D打印工艺,可直接实现多个零件一体化成形;涡轮轴是空腔结构,铂力特在项目历程中对涡轮轴进行了零件特征识别、设计区域划分、拓扑优化盘算和模型重构,实现了整体结构减重约19%。
同时,铂力特还完成了离心叶轮、叶轮盘等零部件的增材制造事情,叶轮盘较薄部位的厚度为0.8mm,铂力特接纳尺寸赔偿控制叶片精度,将偏差控制在0.1mm以内,此叶轮盘零件经超转破裂试验,转速可抵达122000r/min。别的,铂力特还在项目中协助解决了叶片及流道的尺寸控制问题。
在整个项目中,铂力特充分考虑客户需求及航空发动机在结构、性能、工艺、强度、刚度、重量等各方面的要求,开展发动机零件结构集成化、轻量化设计研究,实现庞大零件一体化打印,助力中航发实现“与接纳古板加工工艺的发动机相比,发动机本体零件数减少50%以上,发动机本体减轻质量不低于15%”的项目目标。
3D科学谷Review
在中国航发增材制造发动机项目中,实现发动机减重是重要目标。凭据3D科学谷的市场研究,3D打印带来了通过结构设计层面上抵达轻量化的可行性。具体来说,3D打印通过结构设计层面实现轻量化的主要途径有四种:中空夹层/薄壁加筋结构、镂空点阵结构、一体化结构实现、异形拓扑优化结构。
以上项目中的发动机零部件,在使用古板加工方法制造时由多个零件组装而成,而选区激光熔化3D打印工艺可直接实现多个零件一体化成形,这是3D打印技术实现发动机轻量化的重要途径之一。铂力特在前不久展示了为中国深蓝航天液氧煤油试车发动机所制造的3D打印推力室,推力室的冷却管道直接作为设计中的一部分,在同一生产历程中与整个腔体一起成型,这也是金属3D打印技术在实现功效集成、一体化零件方面的典范应用。
金属3D打印已经成为航空和航空航天领域的一项要害技术,因为它的优势与该行业的要害需求坚持一致,包括减轻重量、节省燃料、提高运营效率、部件整合、加速上市时间和减少对零部件的存储要求。(来源:3D科学谷)
3D打印技术,金属3D打印,3D打印